KAMA ProCut 76
Cutting, creasing, perforating: Whether conventionally or digitally printed ... most print products only really take shape in the finishing stage.
- Die Cutting
- Creasing
- Blind Embossing
- Braille Embossing
- Kiss Cut
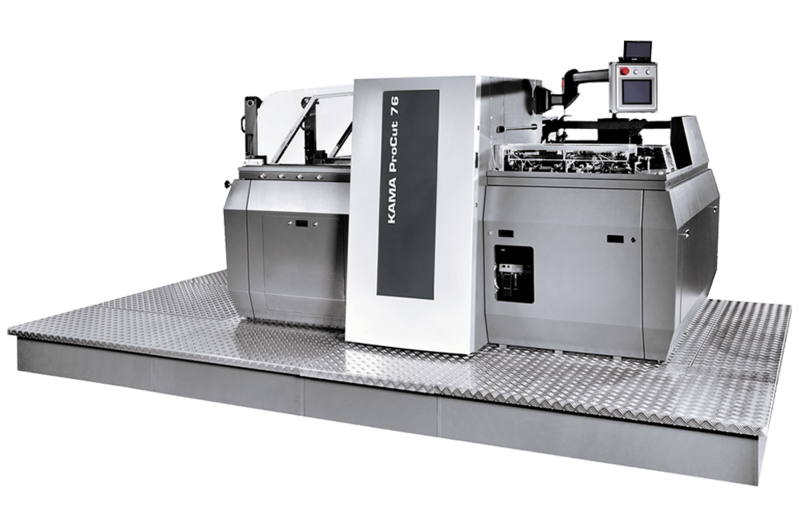
KAMA ProCut 76 die cutter
Short set-up times, time-saving features and high-quality output make the KAMA ProCut 76 flat-bed die cutting and stamping machine a reliable and cost-effective solution for finishing in sheet size B2+ (769 x 600 mm). With the KAMA AutoRegister, you can also cut and crease digitally printed sheets with high registration accuracy, allowing you to address the new market for short runs in packaging.
The versatile ProCut 76 is suitable for many different applications and is a perfect, state-of-the-art successor for worn-out cylinders and platens. And you can simply carry on using any tools you already have. The ProCut 76 can be retrofitted with an hot foil stamping system at any time.
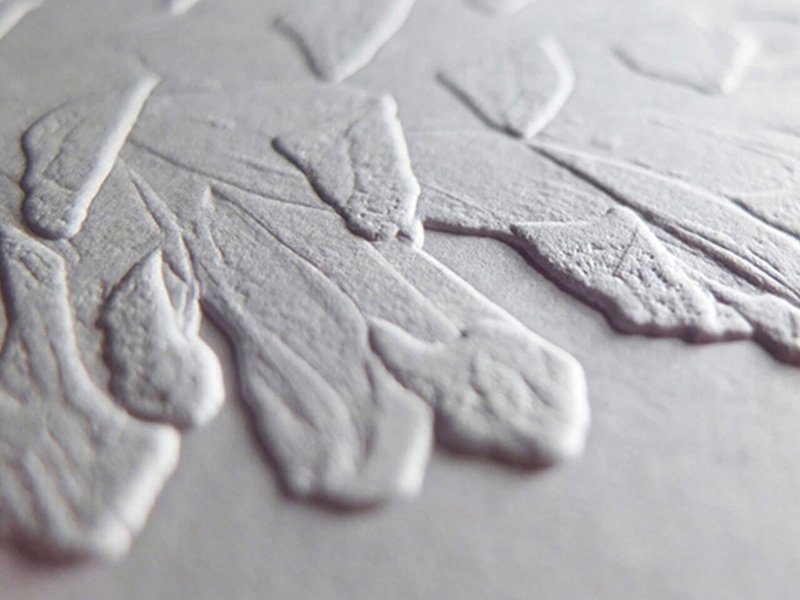
Highlights of the ProCut 76
Versatile applications
Flexible & efficient – for small to medium runs.
Gentle sheet transport on a single level, clean creasing lines, embossing and cutting with highest registration accuracy and no nicks: the ProCut 76 is a flexible solution for post-press finishing of paper, paperboard and plastics in the sheet size B2. The machine can be retrofitted for hot cutting of plastics or for hot foil enhancements.
Fast conversion
Relevant for short runs and digital printing.
Fast order changes are absolutely essential for smaller runs and digitally printed jobs. On the ProCut 76 it takes just around 5 minutes to convert the setup, which means that the next order can start up quickly – thereby making post-press finishing profitable. The 4+1 system with prepared 1 mm plates also ensures that uptime is maximised. With the type of repeat orders involving intensive creasing, which are common in packaging jobs, this can shorten set-up times by up to 90%.
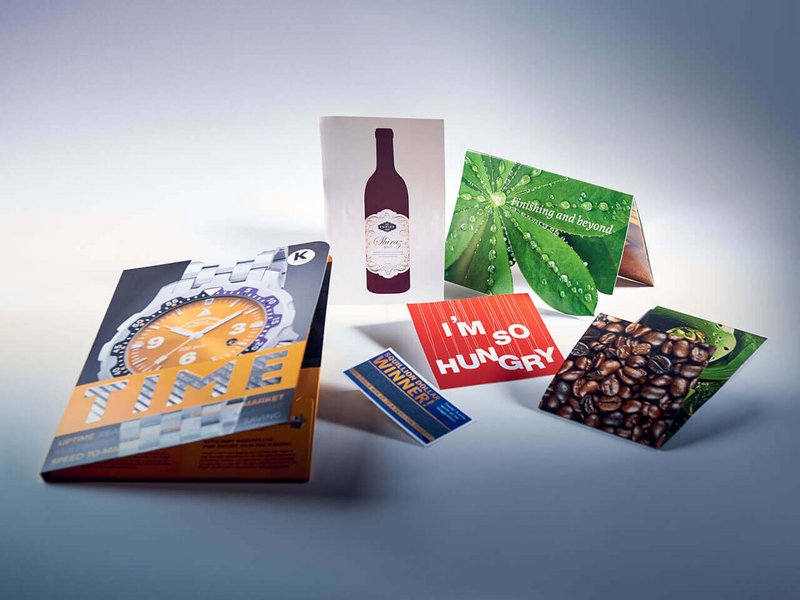
Highest registration accuracy
… for every sheet.
The ProCut 76 machines with the linear KAMA gripper, which doesn't have to be realigned, achieve the best registration accuracy in the market. And the KAMA AutoRegister guarantees the highest precision. It aligns every sheet to the print image, so that all cutting, crease lines and blind embossing is accurately done with an accuracy of a tenth of a millimetre.
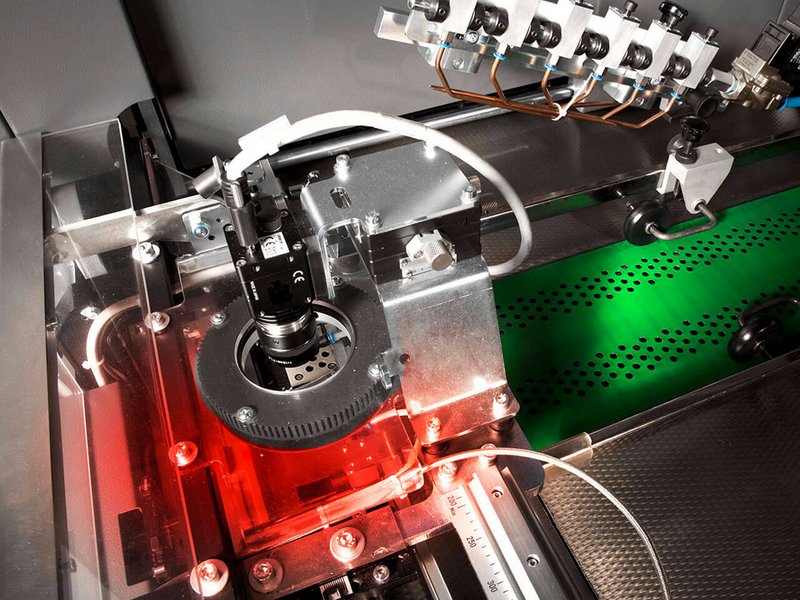
Continue using your existing tools
Smooth transition to the new solution.
Thanks to the universal chase on the ProCut 76, you can continue to use your existing tools without any problems whatsoever. This also applies to small cutting dies.
AutoRegister AR3
NEW: AutoRegister AR3 also provides "skew adjust" - for maximum register accuracy with sheets cut after printing and twisted sheets, for multiple embellishment and most demanding packaging.
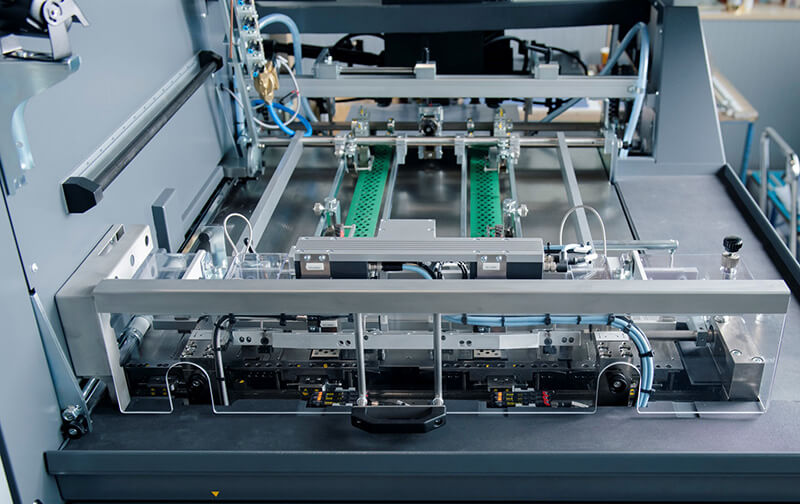
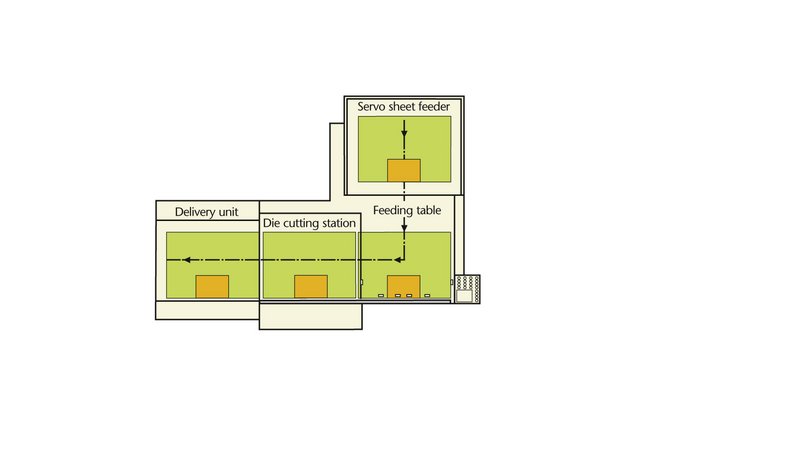
Compact machine
Lots of applications in a small space.
With a footprint of around 12 m2 including the platform, the ProCut 76 makes do with very little space. Sheets are transported at a right angle in the system, so the compact machine can also be positioned in a corner.
Specifications of the ProCut 76
Paper | from 100 g/m² |
Paperboard, micro-corrugated board | max. 1,500 g/m² (bzw. 1.8 mm) |
Plastics (PET, PP, PVC) | max. 1,500 g/m² |
Maximum sheet size | 760 x 600 mm (29 15/16 x 23 5/8 in) |
Minimum sheet size | 279 x 210 mm (11 x 8 1/4 in) |
Speed* | 5,500 sheets/h |
Cutting force | 165 t (1.65 MN) |
Maximum cutting size | 743 x 585 mm (29 3/8 x 23 1/16 in) |
Gripper margin | 10 mm |
Dimensions (length x width) | 4.87 x 2.69 m |
Options
- The KAMA AutoRegister aligns every sheet based on the print image. Perfect for post-press in digital printing.
- Quick-change heating plate system 4+1 for quick job changes
- Universal quick-change heating plate system allows existing tools to still be used
- Magnetic plate for cutting and kiss-cutting of finest contours
- Retrofittable with stamping systems for hot foil and holograms
- Hot-cut system for hot cutting and creasing of plastics
Post-press goes Print 4.0
Digitalising processes, networking machines and establishing integrated workflows.
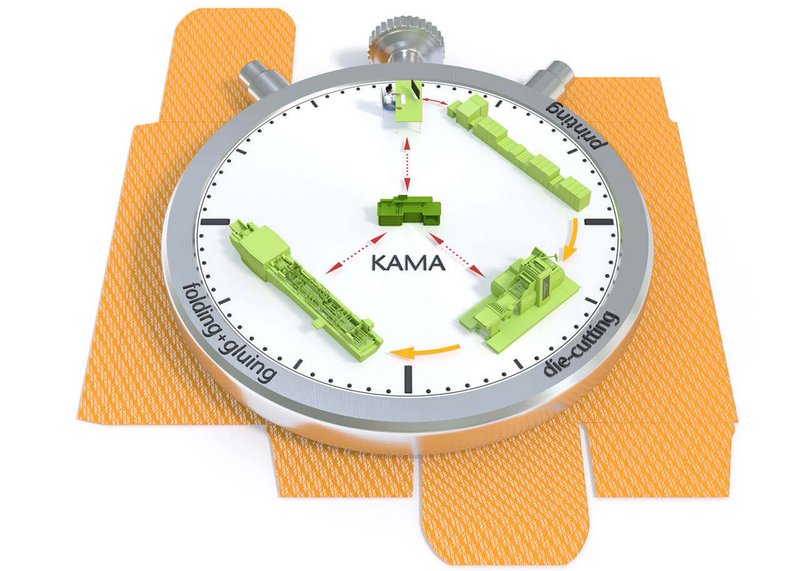
The central element in the KAMA concept for Print 4.0 is its Cockpit with the Job-Manager software. The Job Manager runs on an industrial PC and centrally manages communications with the KAMA machines, while also serving as an interface for networking and integration in the MIS/ERP system of the customer.
Current jobs are received digitally by the Job-Manager software, providing the operator with all the relevant data on the screen with just a few mouse clicks. The Job-Manager generates matching adjustment data for the machines and transmits them there. This simplifies the process of getting the machine ready for the operator and significantly shortens set-up times.
The machines in turn send their data back to the Job-Manager – including set-up time, duration of production, number of good sheets, rejects and of course information about the current status of production. This data can be forwarded to an MIS/ERP system.
Integration in an MIS/ERP system is prepared on a customer-specific basis. We are currently introducing this for reference customer projects both in commercial printing and in packaging.
Once you have integrated the KAMA machines in your network, all aspects of order management can be handled paperlessly and – what is more important – communication errors can be avoided. The processes are better coordinated with each other, helping to eradicate wasted time, costs and movements (“Muda”). The result: significantly shorter throughput times and faster time-to-market.
Particularly when it comes to short and medium runs, we believe that a networked Print 4.0 approach up to and including the post-press stage is absolutely indispensable.
In a nutshell: KAMA Job-Manager software:
- provides networking of KAMA machines for electronic job tickets
- digitalises and accelerates set-up processes
- determines and communicates adjustment data for the tool-free stripper SBU
- determines and transmits adjustment data for optimum foil utilisation during hot foil stamping
- acts as a client for networking with the ERP/MIS
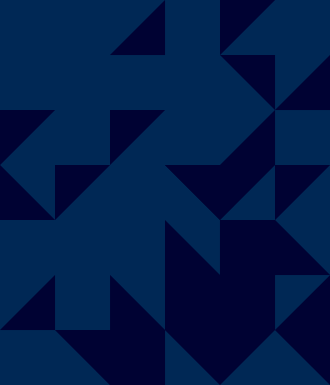