Engineering your success:
Packaging, commercial printing, finishing
For 130 years, engineers at KAMA have been developing high-quality finishing die-cutters as well as folding and gluing machines for the global market.
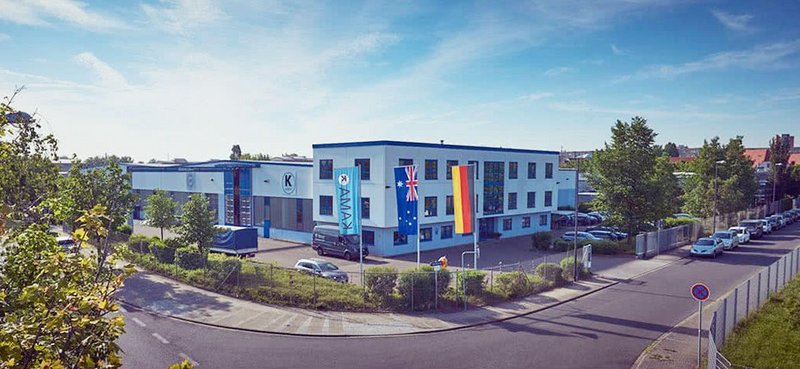
Cutting and finishing machines from KAMA are in demand worldwide
As a well-established, reliable partner for cutting and finishing processes, we offer a wide range of profitable solutions for small and medium-sized conventional print runs as well as for digital printing. With more than 800 installations in 80 countries the innovative KAMA machines "made in Germany" are in demand around the world - in the commercial print market and also in packaging.
From the company’s early days with 20 employees when it was founded after the reunification of Germany, it has now grown to 110 members of staff.
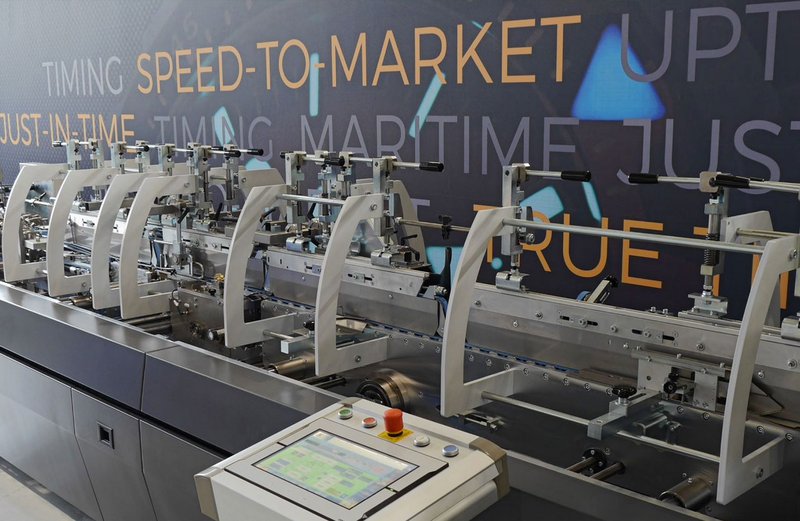
KAMA Product families
Trust defines partnerships
Our customers are job printers, print finishing companies, bookbinders and more and more packaging manufacturers - small and medium-sized as well as well-known large companies around the world.
We distribute our machines in close co-operation with leading printing machine manufacturers and sales organisations. You can reach us directly wherever you are.
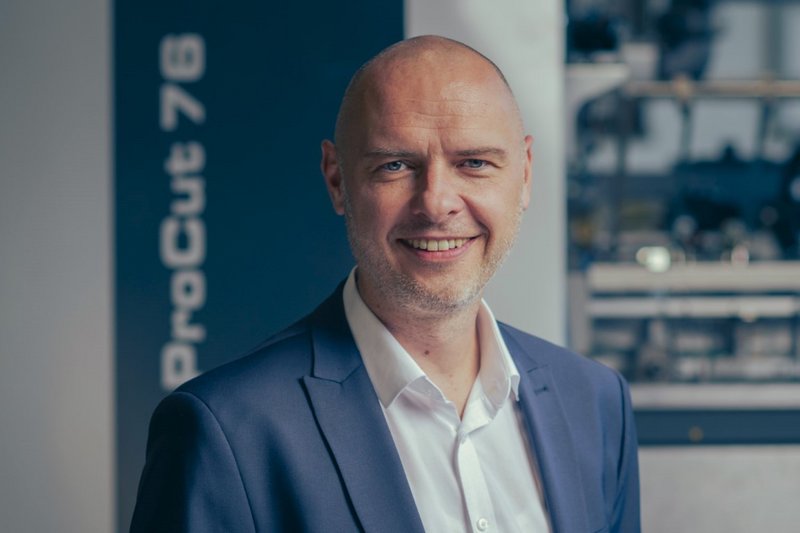
Facts and figures
Re-establishment | 1994 in the form of a limited liability company (GmbH), based on the 100-year old companies SCAMAG/Polygraph KAMA in Dresden |
---|---|
Managing Director | Robert Löchel |
Business fields | Development and construction of automatic die cutters, hot foil and hologram stamping modules, hot-cut modules, folder-gluers, production of complex assemblies for finishing |
Employees | About 110 technicians and engineers, plus trainees |
Location | Dresden/Germany – design and production departments |
Certification | Since 2000: certified to DIN ISO 9001 for the production of machine and engineering components |
Milestones in the development of the company
1894 | Company founded in Dresden under the name Sächsische Cartonnagen-Maschinen-Actiengesellschaft SCAMAG |
---|---|
1936 | Development of the “Tempo”, the first automatic flat-bed die cutter in the world with sheet feeder and delivery unit |
1972 | Launch of the newly designed folder-gluer FKM 100 |
1994 | KAMA is re-established as a limited liability company (GmbH) by Marcus Tralau, now member of the Advisory board for strategic issues |
1999 | Launch of the completely newly developed KAMA TS 74 product series of feature-rich automatic die cutters |
2000 | Relocation of the administration, development and production departments to the company’s own newly-built offices and buildings in the Reick district of Dresden |
2002 | Construction of a second production hall and doubling of production space to 4,000 m² |
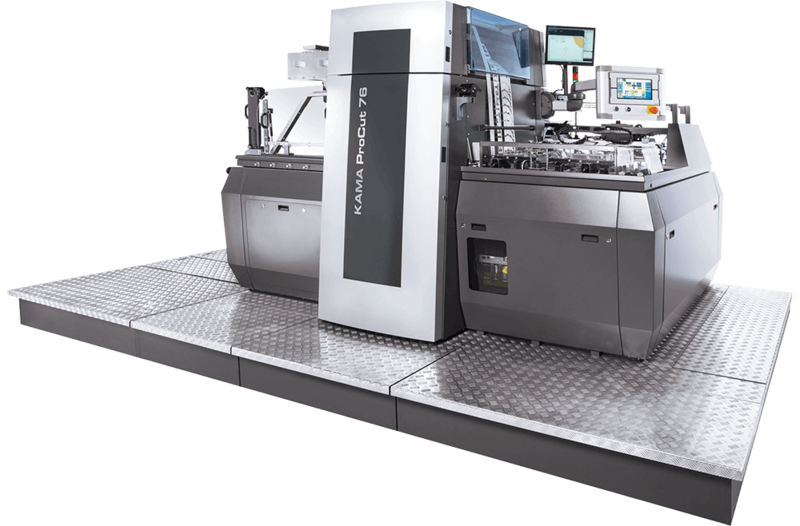
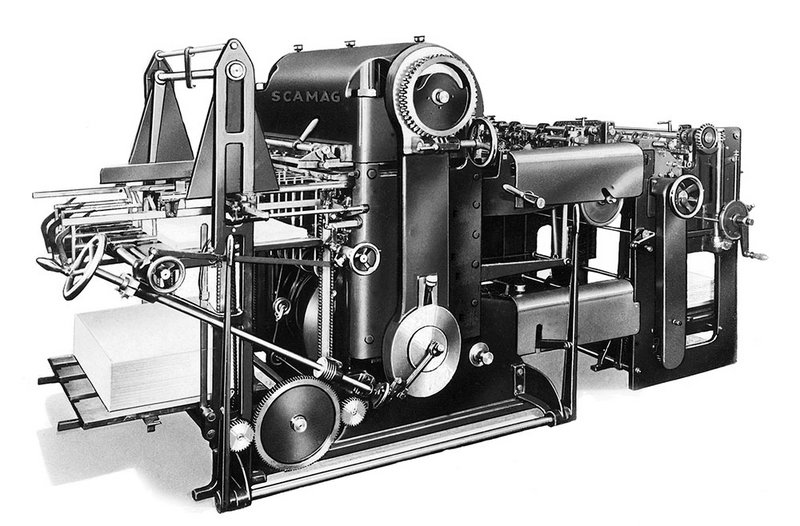

Every KAMA machine contains a glimpse of the future
Just like our customers, we see the changes that are taking place in our dynamic industry as a source of motivation and an opportunity to grow. This is why 10 percent of our employees work in the area of research and development. They make sure that every KAMA machine contains a glimpse of the future – to help you successfully manage the requirements in post-press, finishing and print enhancements.
Cooperation projects with TU Dresden, the Leipzig University of Applied Sciences and other players guarantee fast knowledge transfer from research into practice.
Some innovations from the past 20 years at a glance
2017 | KAMA expands the JobManager software for machine networking, process optimisation and automation. |
---|---|
2016 | At drupa the Dresden-based company presents the “Generation Servo” of the ProCut 76 Foil with doubled output for hot foil stamping. |
2015 | KAMA launches the first fully automatic folder-gluer FlexFold 52i. Changeovers at record speed make the production of digitally printed packaging and small SKU's profitable. |
2014 | KAMA presents the SBU inline stripper for tool-free stripping and blank separation. |
2012 | KAMA launches the AutoRegister. It ensures precise registration accuracy for each sheet – also with digital printing. |
In the same year the company also presents the new ProCut 76 Foil, with new features, a servo-driven sheet feeder and the larger sheet size of 760 x 600 cm. | |
2010 | The “JobPlanner” is released for software-supported setup of the ProFold 74 folder-gluer. |
2008 | At drupa KAMA presents the world’s first die cutting machine for the classical digital print format: ProCut 58. |
2007 | KAMA launches the ProFold 74 folder-gluer with a patented, grid-controlled tool mounting system. |
2006 | New design for the ProCut 74 finishing die cutter, with new options and higher output. A device for hologram stamping is also developed. |
2005 | The hot-cut system for cutting plastic materials on KAMA ProCut die cutting machines is ready for market. |
2002 | KAMA launches a hot foil stamping module for the ProCut models; since then, these have been the die cutting and finishing machines with the widest range of applications. |
Multimedia booklet
With 360° panorama, machine videos & what our solutions can do for you!
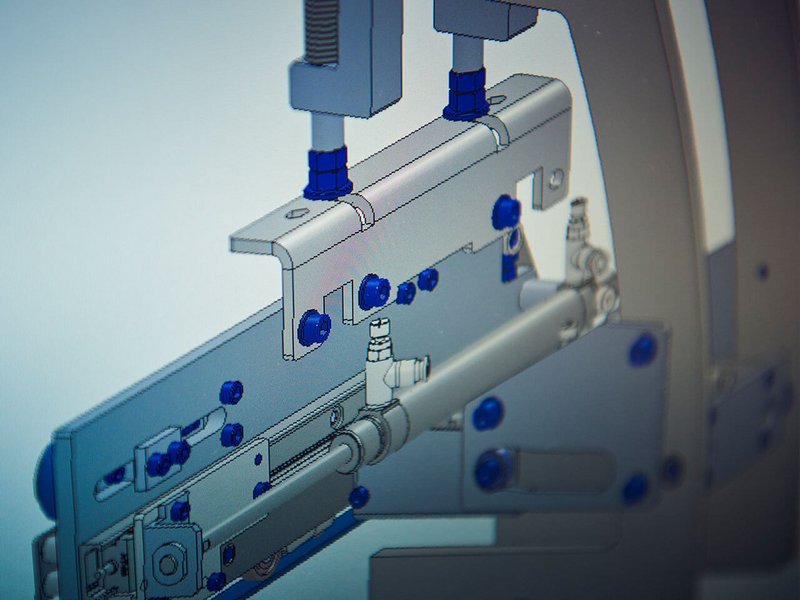
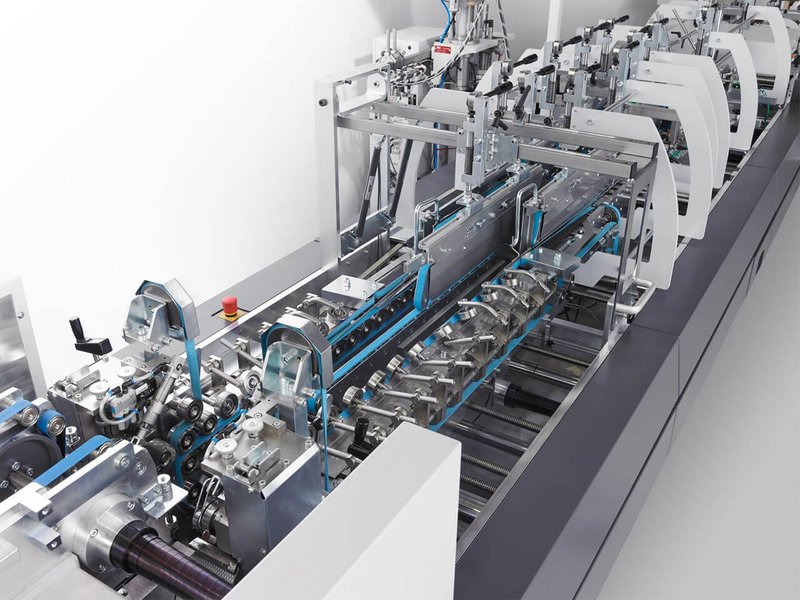
Precision in production
Even if KAMA die cutting machines are sturdy “heavy metal constructions” that weigh in at several tonnes, highest levels of precision are the key when it comes to the individual parts and components.
In our DIN ISO 9001 certified production department, we use state-of-the-art CNC machining centres to manufacture all key machine and engineering components in-house. Complete assembly of the die cutting and finishing machines and folder-gluers as well as quality assurance with the latest measuring equipment are also performed at our site in Dresden.
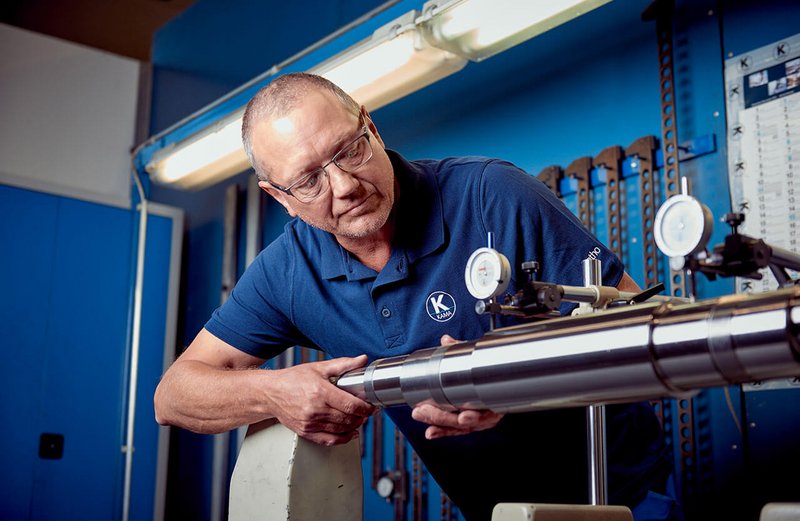
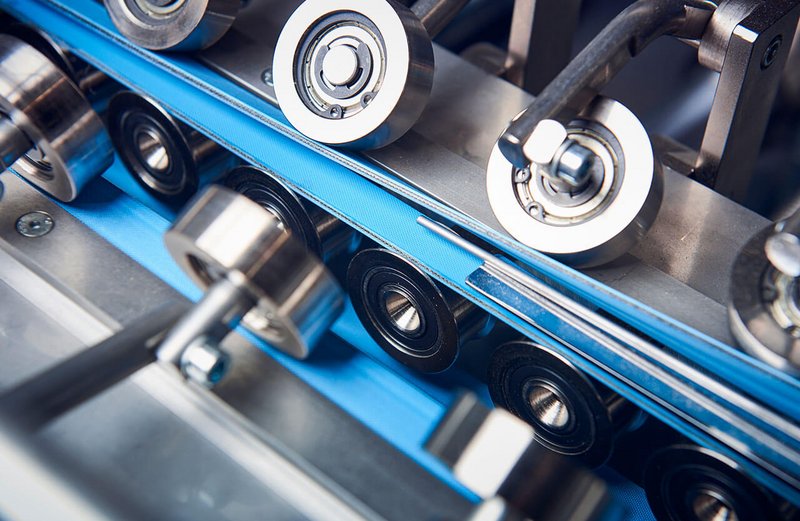
More precise than clockwork? Exactly!
When it comes to components like grippers, guide rails in the cutting head and crankshafts, production is even more precise than for a high-precision watch movement – if the relevant proportions are taken into account. For example, the tolerance of the crankshaft in a ProCut cutter is just one hundredth of a millimetre. Although it may be perhaps one ten-thousandth in a watch movement, the cutter wins in relation to its overall size.
Short paths to innovation
Design and implementation: the high vertical range of manufacture at KAMA means that ideas and improvements can be quickly implemented so that product development can be driven forwards.